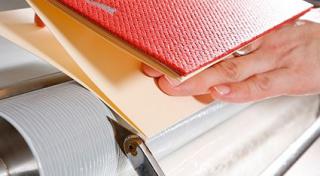
Litho-laminating is one of the post-printing processes. The technology involves gluing a rather thin printed material (liner) to a thicker and rigid basis. A coated paper (from 115 gsm or higher) or cardboard (up to 250 gsm) can be used as a liner and it can also be varnished or laminated if you wish it.
For basis we use corrugated cardboard, micro-corrugated cardboard (two- or three-layered) Kappa cardboard, bookbinding cardboard of any thickness (cardboard-to-cardboard gluing). Up to 3 mm thick cardboard or micro-corrugated cardboard is used as a basis. Depending on the number of liners, this process may be single-sided or two-sided. In some cases we use vinyl binding materials, creative papers or some types of films, plastic and other materials.
Litho-laminating is used for POS-materials and packaging, i.e. for items weighing over 1 kg such as glassware, tableware, electrical appliances, etc.
Thanks to this technology, printed products have bright, presentable appearance and extra durability and safety features. Litho-laminating is also good when you need to combine high-quality printed output and excellent solidity.
Ulmapress applies litho-laminating to produce a variety of boxes for different products: boxes for perfumes, tableware and glassware, tables games, POS-displays, etc. Litho-laminated cardboard and micro-corrugated cardboard not only guarantees safety transportation of your products, but also enhance the image of your company, attracting the attention of potential customers. We’ll find the best post-printing solution for you and qualitatively perform litho-laminating of any complexity!